In the world of manufacturing and industrial processing, cutting tools are the unsung heroes that drive productivity and efficiency. From metalworking to woodworking, and from plastics to composites, cutting tools are essential for shaping, sizing, and finishing a wide range of materials. Among the various materials used to make these tools, tungsten carbide (WC) stands out for its exceptional properties that significantly enhance the performance of cutting tools.
Tungsten carbide is a hard, wear-resistant material composed of tungsten and carbon atoms bonded together in a crystalline structure. This unique composition gives tungsten carbide its remarkable hardness and durability, making it an ideal choice for cutting tool applications.
One of the primary ways tungsten carbide improves cutting tool performance is through its high hardness. With a hardness rating that rivals diamonds, tungsten carbide blades and tips can withstand the intense pressures and frictions generated during the cutting process. This allows them to maintain their sharpness for longer periods, reducing the frequency of sharpening and tool replacement.

In addition to hardness, tungsten carbide's wear resistance is another key factor in improving cutting tool performance. Wear resistance refers to a material's ability to resist gradual removal of its surface due to mechanical action, such as friction or abrasion. Tungsten carbide's wear resistance ensures that cutting tools retain their original shape and dimensions, even after prolonged use. This consistency in tool geometry leads to more accurate and predictable cutting results, enhancing overall process control and product quality.
Tungsten carbide's high thermal stability also contributes to its suitability for cutting tool applications. During the cutting process, friction between the tool and the workpiece generates heat, which can cause thermal expansion and softening of the tool material. Tungsten carbide's ability to maintain its hardness and strength at elevated temperatures ensures that cutting tools remain effective even under demanding conditions.
Moreover, tungsten carbide's chemical inertness makes it resistant to corrosion and attack by various chemicals and environments. This property is particularly important in cutting tools used in corrosive or abrasive environments, where traditional materials may degrade rapidly.
The combination of these properties allows tungsten carbide cutting tools to offer significant advantages over traditional materials such as high-speed steel and tool steel. They can achieve higher cutting speeds, longer tool life, and better surface finish quality. This, in turn, leads to increased productivity, reduced downtime, and lower overall costs.
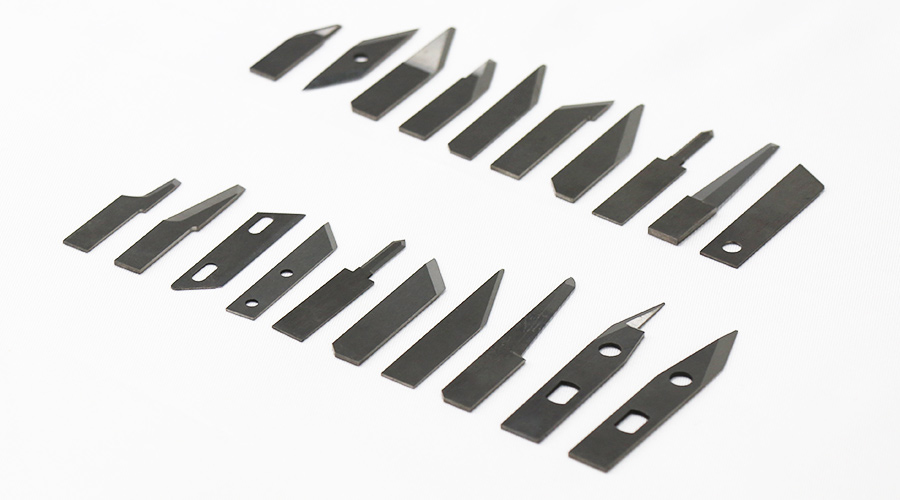
In conclusion, tungsten carbide is a game-changer in the realm of cutting tools. Its exceptional hardness, wear resistance, thermal stability, and chemical inertness make it an ideal material for manufacturing high-performance cutting tools that can meet the demands of modern manufacturing processes. As technology continues to evolve, tungsten carbide will undoubtedly play an increasingly important role in shaping the future of cutting tool technology.
Later, We will continue to update information about industrial blades, and you can find more information on our website (passiontool.com) blog.
Of course, you can also pay attention to our Official social media:
Post time: Feb-17-2025