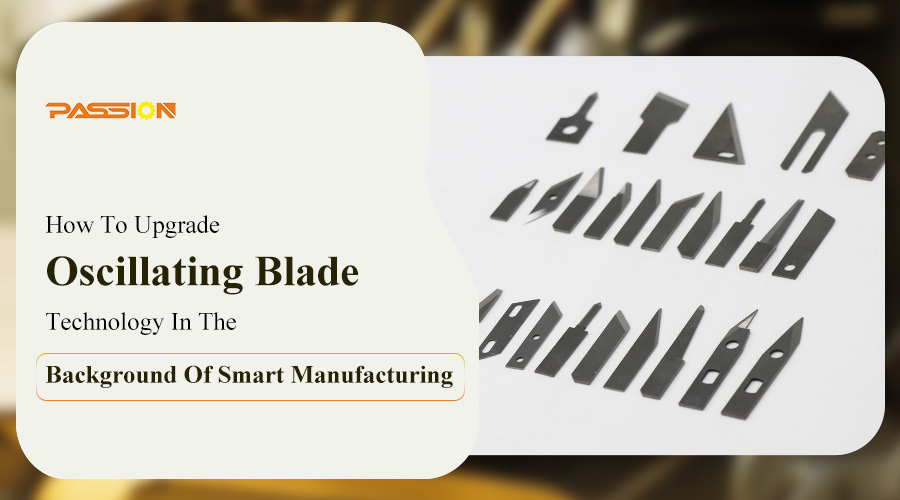
With the rapid development of intelligent manufacturing technology, the traditional cutting process is undergoing unprecedented changes. Among them, oscillating blade technology, as an emerging technology with significant advantages, is being continuously upgraded and improved to meet the demand for high-precision and high-efficiency machining in the context of smart manufacturing.
Oscillating blade technology, through the high-frequency vibration of the blade in the cutting process, greatly improves the cutting efficiency and precision. Traditional blades often suffer from high friction and elevated temperatures during cutting, resulting in low cutting efficiency and poor workpiece surface quality. Oscillating blade technology, on the other hand, uses a built-in motor to drive the blade to vibrate rapidly, which reduces friction and makes cutting more labor-saving and efficient. This technology is not only suitable for flexible and semi-rigid materials, but also shows great potential in the field of metal processing.
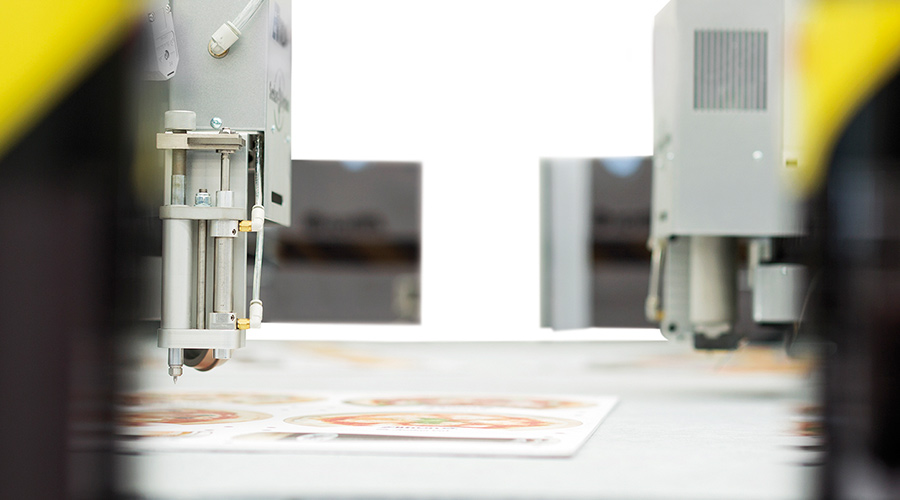
In the background of smart manufacturing, the upgrade of oscillating blade technology is mainly reflected in the following aspects:
First, the introduction of intelligent control system makes oscillating blade technology more flexible and intelligent. Through the deep integration with the CNC system, the oscillating blade technology can adjust the cutting parameters in real time to ensure the stability and accuracy of the cutting process. In addition, the interaction with virtual machining software makes it possible to display the grinding wheel and workpiece machining trajectory in real time on the PC of the CNC system after generating the code, effectively verifying the correctness of the code and improving production efficiency and product quality.
Secondly, the thermal coupling model of oscillating blade technology is being continuously improved. In the cutting process, the thermal interaction between the blade and the workpiece is a complex process involving the coupling of multiple fundamental fields such as temperature, displacement and fluid. By establishing a more accurate finite element model, various physical phenomena in the cutting process can be simulated more accurately, providing strong support for optimizing cutting parameters and improving cutting quality.
In addition, oscillating blade technology has made significant progress in material adaptability. Traditional blades are often only cut for specific materials, while oscillating blade technology can realize the cutting of a variety of materials by adjusting the vibration frequency and cutting parameters. This not only expands the range of applications, but also improves productivity and flexibility.
Finally, with the increasing awareness of environmental protection, oscillating blade technology has also made significant progress in environmental protection. Traditional cutting methods often produce a large amount of dust and noise pollution, while oscillating blade technology through high-frequency vibration and precise control, to achieve a smoke-free, odorless and dust-free cutting process, effectively reducing the impact on the environment.
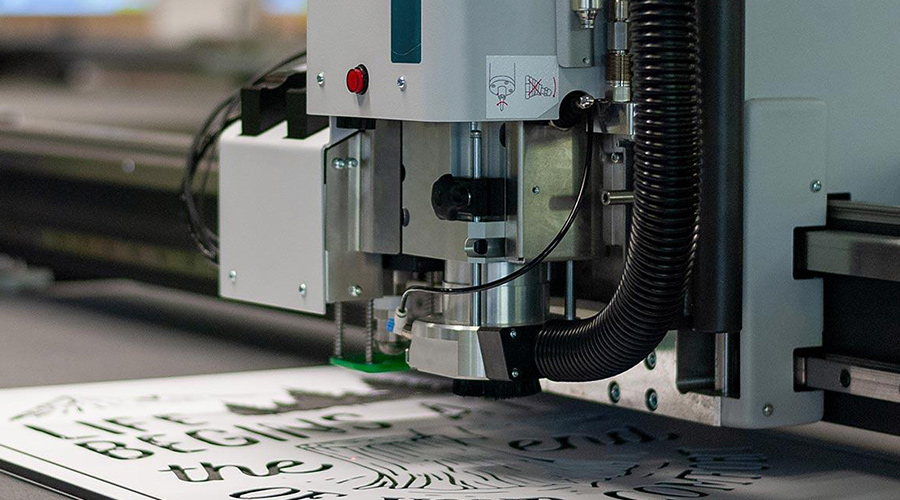
In summary, oscillating blade technology is experiencing comprehensive upgrading and change in the context of intelligent manufacturing. Through the introduction of intelligent control system, improvement of thermal coupling model, improvement of material adaptability and enhancement of environmental performance, oscillating blade technology is gradually becoming one of the important supporting technologies in the field of intelligent manufacturing. In the future, with the continuous progress of technology and the expansion of application fields, oscillating blade technology will play a more important role in the field of intelligent manufacturing.
Later, We will continue to update information, and you can find more information on our website (passiontool.com) blog.
Of course, you can also pay attention to our Official social media:
Post time: Nov-25-2024