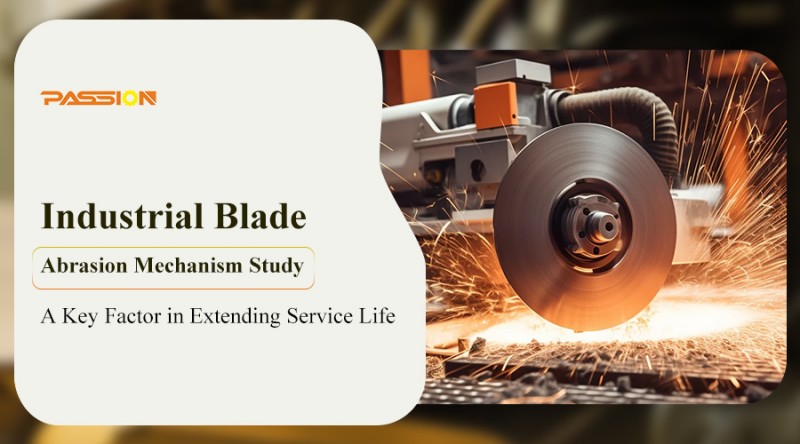
In the field of industrial manufacturing, blade abrasion has always been an important factor affecting productivity and product quality. With the progress of science and technology and the continuous optimization of the process, the research on industrial blade abrasion mechanism is becoming more and more in-depth, aiming to find the key factors to extend the service life of the blade.

There are various reasons for blade abrasion, mainly including mechanical wear, thermal wear, chemical wear and diffusion wear. Mechanical abrasion is mainly caused by the hard particles in the workpiece material to make grooves on the blade surface, and this kind of abrasion is especially obvious when cutting at low speeds. Thermal abrasion is due to a large amount of heat generated during the cutting process, resulting in plastic deformation of the blade abrasion or thermal cracks. Chemical wear is the oxygen in the air at high temperatures and the chemical reaction of the blade material, the formation of low hardness compounds, the chip away, resulting in blade abrasion. Diffusion abrasion, on the other hand, is that during the cutting process, the chemical elements on the contact surface of the workpiece and the blade abrasion diffuse with each other in the solid state, changing the compositional structure of the blade and making its surface layer fragile.
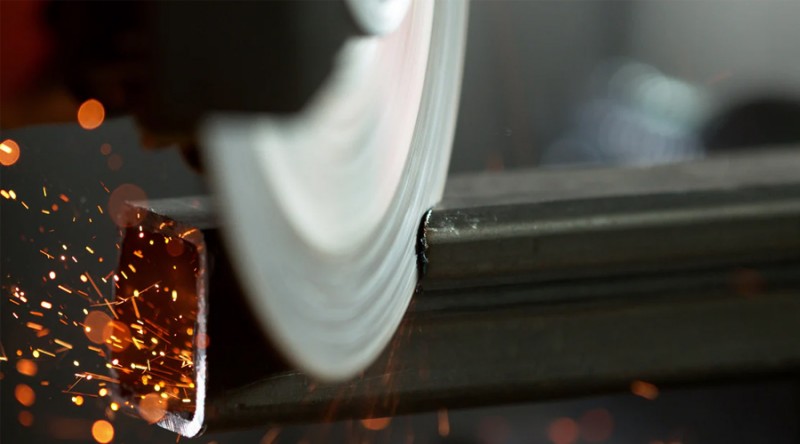
For these wear mechanisms, researchers have proposed a variety of methods to extend the service life of the blade abrasion. First of all, reasonable selection of blade materials is the key. According to the characteristics of the processed material and cutting conditions, selecting a blade material with sufficient hardness, wear resistance and toughness can effectively reduce abrasion. For example, when machining difficult-to-cut materials with a large tendency to harden, the blade material with strong resistance to cold welding and strong resistance to diffusion should be selected.
Secondly, optimizing blade geometry parameters is also an important means of extending service life. Reasonable blade angle and blade shape can reduce cutting force and cutting heat, and reduce blade abrasion. For example, appropriate reduction of the front and back angles and the use of a larger negative edge inclination can reduce the wear of the cutting edge. At the same time, grinding a negative chamfer or edge arc can also enhance the strength of the tip of the blade and prevent chipping.
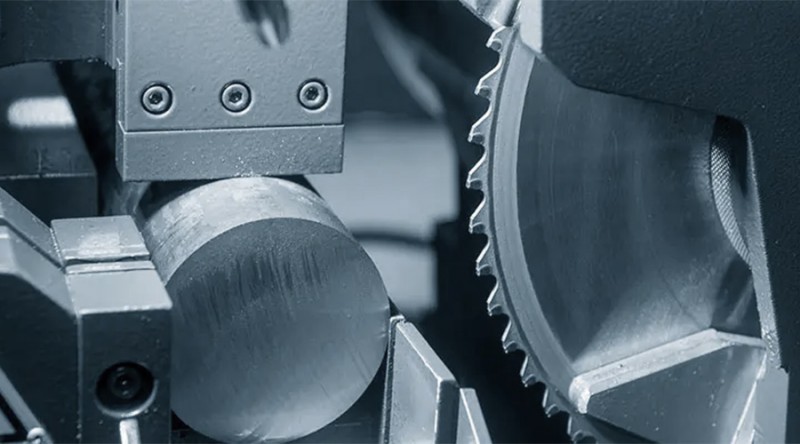
In addition, reasonable selection of cutting dosage and the use of cooling lubricant is also an effective way to extend blade life. The depth of cut and feed are too large, the cutting force increases, and the blade abrasion is accelerated. Therefore, under the premise of ensuring processing efficiency, the cutting amount should be minimized. At the same time, the use of cooling lubricants can absorb and take away most of the heat in the cutting zone, improve the heat dissipation conditions, reduce the cutting temperature of the blade and workpiece, thus reducing blade abrasion.
Finally, the correct operation method and process system rigidity are also factors that cannot be ignored. In the cutting process, the blade should try to make the blade does not bear or less bear the sudden change of the load, to avoid the blade due to uneven force and breakage. At the same time, to ensure that the process system has a good rigidity, reduce vibration, can also effectively extend the service life of the blade.
In summary, the key factors to extend the service life of industrial inserts include reasonable selection of blade materials, optimization of blade geometry parameters, reasonable selection of cutting dosage, the use of cooling lubricants and the correct operating methods and process system rigidity. With the continuous deepening of the research on the mechanism of blade abrasion, it is believed that more innovative technologies and methods will appear in the future, injecting new vitality into the development of the industrial manufacturing field.
Later, We will continue to update information, and you can find more information on our website (passiontool.com) blog.
Of course, you can also pay attention to our Official social media:
Post time: Nov-15-2024