
Preface
Blade coating technology is one of the key technologies in the field of modern cutting blade manufacturing, and materials and cutting process known as the three pillars of cutting blade manufacturing. Coating technology through the blade substrate coated with one or more layers of high hardness, high wear-resistant materials, significantly improve the blade's wear resistance, oxidation resistance, anti-adhesion, thermal shock resistance and other comprehensive performance, so as to extend the life of the blade, improve cutting efficiency and machining accuracy.
Coating material
Maintaining slotter blades in optimal condition is essential for prolonging their lifespan and ensuring consistent performance. Proper maintenance includes regular cleaning, inspection for wear or damage, and timely sharpening or replacement of blades as needed. Keeping the blades clean from debris and coolant buildup prevents premature wear and maintains cutting precision. Inspecting blades for any signs of wear, such as chips or dull edges, allows for timely maintenance to avoid costly damage to the workpiece. Sharpening or replacing blades when necessary ensures efficient cutting and prevents quality issues in the machined parts.
There is a wide range of blade coating materials, mainly including carbide, nitride, carbon-nitride, oxide, boride, silicide, diamond and composite coatings. Common coating materials are:
(1)TITANIUM NITRIDE COATING
Titanium nitride coating, or TiN coating, is a hard ceramic powder with a golden yellow colour that can be applied directly to the substrate of a product to form a thin coating.TiN coatings are commonly used on blades made of aluminium, steel, titanium alloys and carbide.
TiN coatings are rigid materials that increase the hardness and durability of inserts, as well as resisting wear and friction. the cost of TiN is typically low, which makes it ideal for manufacturers looking for a cost-friendly solution.
(2)TITANIUM CARBON NITRIDE
TiCN is a coating that combines titanium, carbon and nitrogen to form a coating that helps strengthen industrial blades. Many of the applications are the same as TiN coatings, however, TiCN coatings can perform better in specific applications with higher surface hardness, and are often chosen when cutting harder materials.
TiCN is an environmentally friendly coating that is non-toxic and FDA compliant. The coating has strong adhesion and can be applied to a wide variety of materials. Industrial blades coated with TiCN have a silvery grey colour, which not only provides high corrosion and wear resistance, but also extends the life of the blade by withstanding lower temperatures and reducing damage (e.g., splintering) that occurs during normal operation.
(3)DIAMOND-LIKE CARBON COATING
DLC is a man-made material with properties similar to those of natural diamonds, greyish-black in colour and highly resistant to corrosion, abrasion and scuffing, DLC coatings are applied to blades in the form of a vapour or gas, which cures to help improve the protective features of industrial knives.
DLC is thermally stable up to about 570 degrees Fahrenheit, making it ideal for use in extreme temperatures and conditions, and DLC coatings also help industrial knives combat surface degradation caused by a variety of factors such as humidity, oil and salt water.
(4)TEFLON BLACK NONSTICK COATING
Teflon black non-stick coatings are commonly used on industrial blades to reduce the build-up of sticky surfaces, foodstuffs and plastics, and this type of coating offers many benefits, including excellent abrasion and corrosion resistance, and is also FDA-approved, making it ideal for the food processing industry.
(5)HARD CHROME
Hard chrome is a commonly used coating in the finishing process. Hard chrome coatings resist corrosion, abrasion and wear, making it one of the most effective coatings in a variety of industries.Hard chrome is ideally suited to materials such as steel as it helps to resist corrosion and oxidation while still helping to maintain surface hardness.
(6)POLYTETRAFLUOROETHYLENE
PTFE is a highly flexible coating with excellent resistance to most elements. With a melting point slightly above the 600 degree Fahrenheit range, PTFE can perform over a wide range of temperatures. PTFE is also resistant to chemicals and has low electrical conductivity, allowing it to be used as a blade coating for a variety of applications.
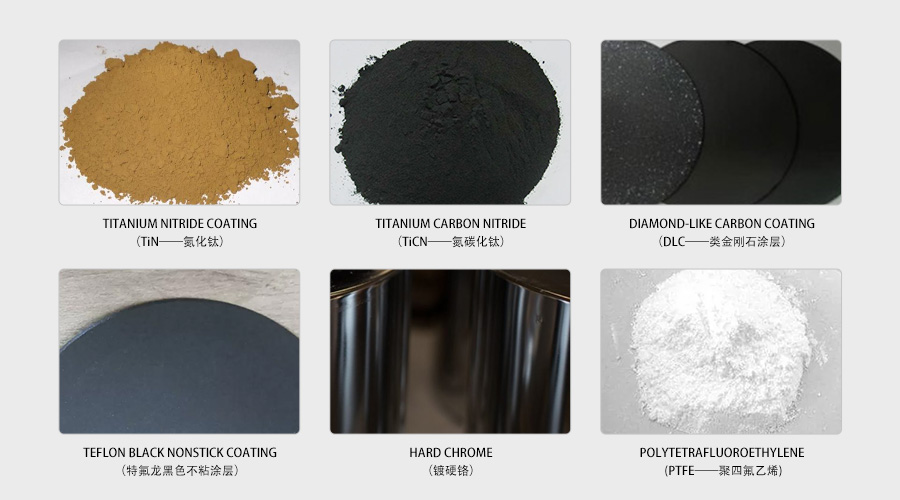
In addition, there are a variety of coating materials such as CrN, TiC, Al₂O₃, ZrN, MoS₂, and their composite coatings such as TiAlN, TiCN-Al₂O₃-TiN, etc., which are able to further enhance the comprehensive performance of the blades
That's all for this article. If you need the industrial blades or have some questions about it, you can contact us directly.
Later, We will continue to update information, and you can find more information on our website (passiontool.com) blog.
Of course, you can also pay attention to our Official social media:
Post time: Sep-27-2024