In the packaging industry, the production and processing of corrugated cartons place high demands on the wear resistance, hardness and sharpness of cutting tools. Over the years, Tungsten Carbide has become the material of choice for corrugated slitter knives due to its excellent physical and chemical properties. In this article, we look at what makes tungsten carbide stand out from the crowd as the best choice for corrugated slitter knives.
Tungsten carbide, also known as tungsten carbide, is an alloy material made through a powder metallurgical process. It consists of tungsten carbide and cobalt and other metal binders, and has a series of excellent properties such as high hardness, high wear resistance, high strength and corrosion resistance. These properties make tungsten carbide cutting blades excellent in dealing with corrugated boxes, a high hardness, high strength material.
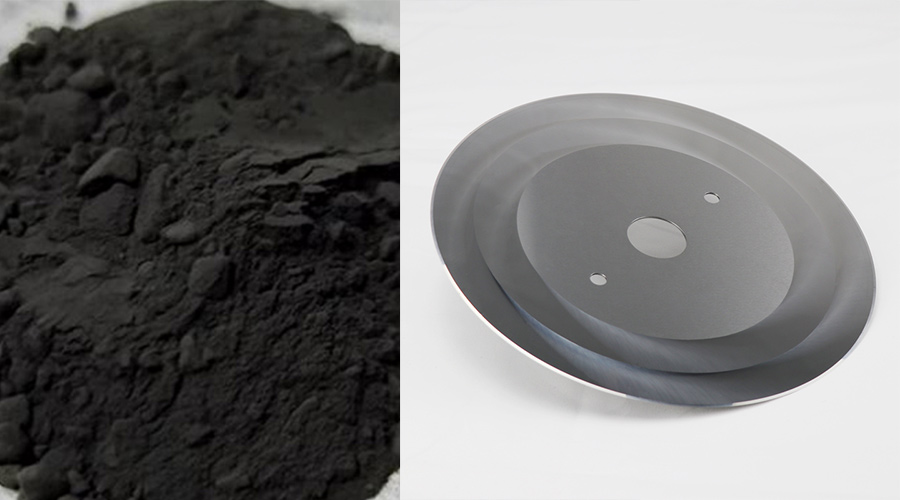
The cutting process of corrugated boxes requires blades with extremely high wear resistance. Tungsten carbide tools have significantly better wear resistance than traditional blade materials such as high-speed steel and stainless steel. This means that tungsten carbide blades have a longer service life, resulting in less downtime and increased productivity. For the packaging industry, this means lower maintenance costs and higher throughput.
Tungsten carbide's high hardness is also a key reason why it is an ideal material for corrugated box cutting blades. Hardness is a measure of a material's ability to resist scratches and indentations. During the cutting of corrugated boxes, the blade needs to withstand high intensity pressure and friction. Tungsten carbide's hardness is much higher than that of other traditional cutting blade materials, which enables it to maintain the sharpness of the edge over a long period of time, ensuring cut quality.
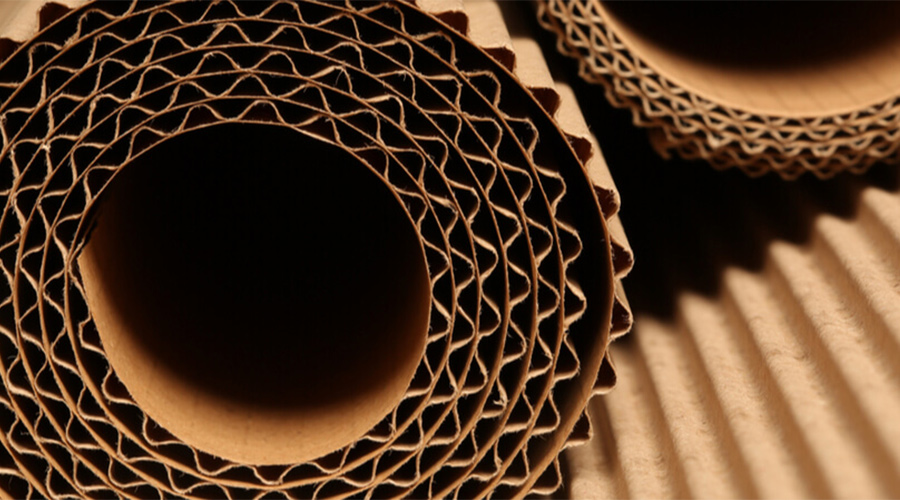
In addition to wear resistance and hardness, tungsten carbide also has good thermal conductivity. During the cutting process, the blade generates heat, and if the heat cannot be dissipated in time, it will lead to deformation of the blade and dulling of the edge. The thermal conductivity of tungsten carbide helps to reduce the thermal effect during the cutting process, maintaining the stability of the blade and cutting accuracy.
Tungsten carbide blades are also able to achieve efficient and precise delamination cutting effects during the corrugated box cutting process. This is essential to prevent material from separating between layers or rupturing at the edges. Especially in ultrasonic cutting technology, the excellent performance of tungsten carbide blades is given full play, further enhancing the overall efficiency and processing quality of cutting.
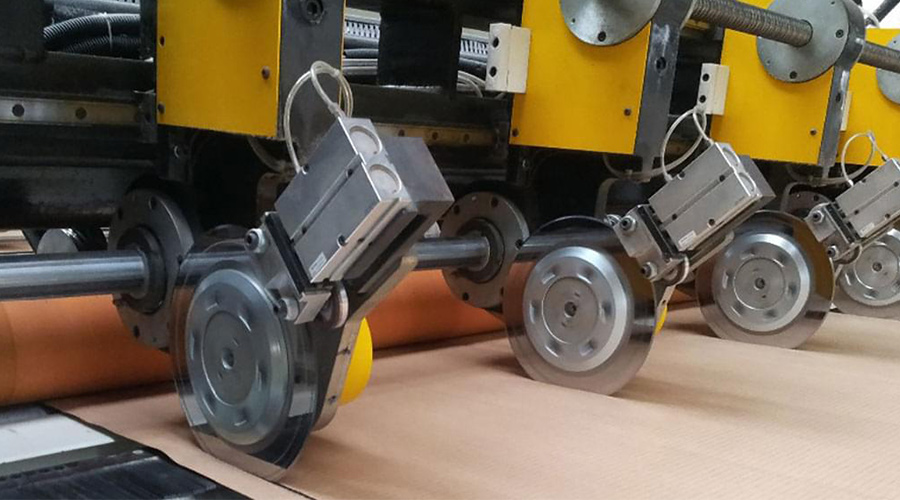
In summary, tungsten carbide is the best material for corrugated paper cutting blades due to its high hardness, high wear resistance, high strength and good thermal conductivity. It not only improves productivity and reduces maintenance costs, but also ensures cutting quality and precision. With the continuous development of blade design and material science, the application of tungsten carbide blades in the packaging industry will have a broader future, providing better solutions for efficient and precise processing.
Later, We will continue to update information, and you can find more information on our website (passiontool.com) blog.
Of course, you can also pay attention to our Official social media: